Multi Way Ball Valve
A multi-way ball valve is a type of valve that has multiple ports, allowing for the flow of fluid to be redirected in different directions. It is typically made from stainless steel and has a ball inside with multiple holes that can be aligned with different ports to control the flow of fluid.
Multi-way ball valves are commonly used in applications where the flow of fluid needs to be redirected or controlled in multiple directions, such as in chemical processing, oil and gas, and water treatment industries. They are also used in applications where space is limited and multiple valves would be impractical.
Multi-way ball valves come in various configurations, including 3-way, 4-way, and 5-way valves, with each configuration having a different number of ports. They are also available in different sizes and pressure ratings to suit different applications. These valves are known for their durability and reliability, making them a popular choice for many different industries.
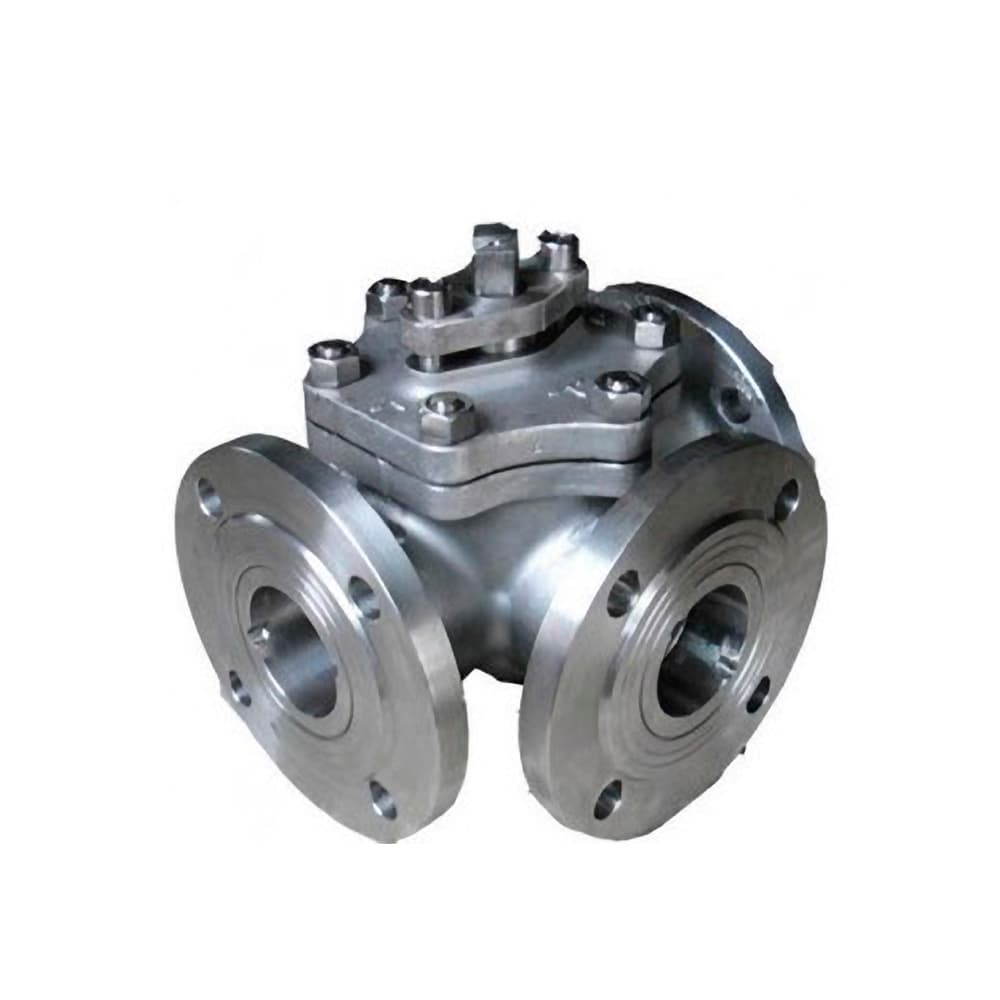
Three Way Ball Valve
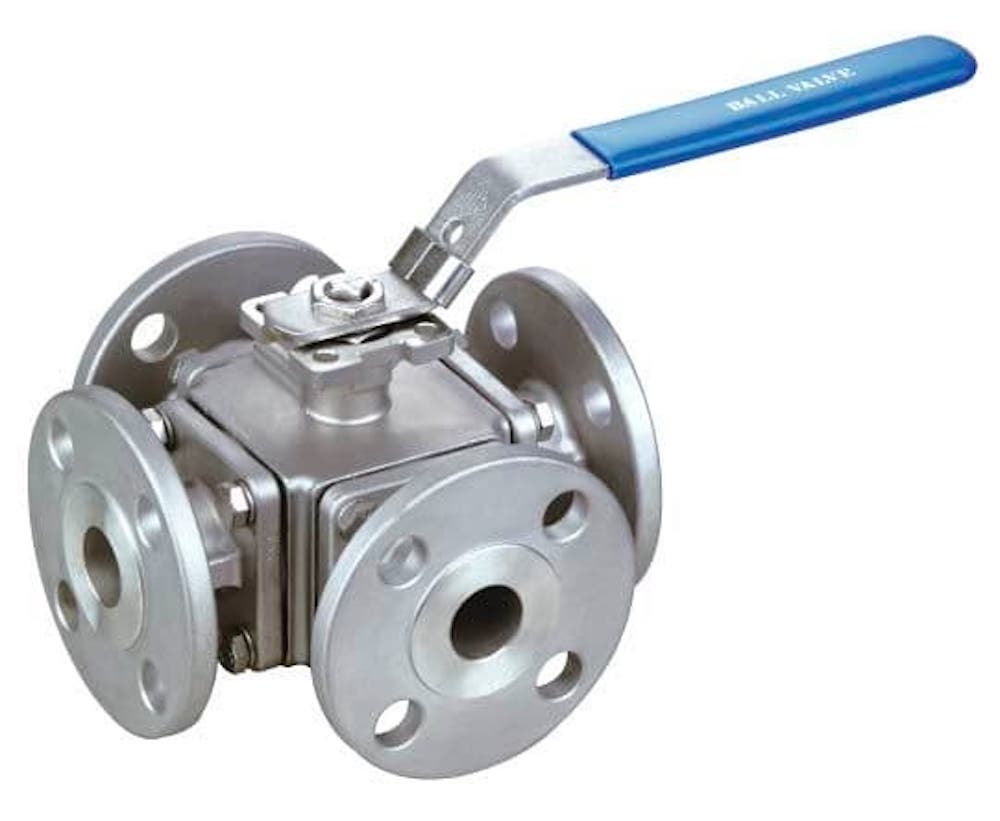
Four Way Ball Valve
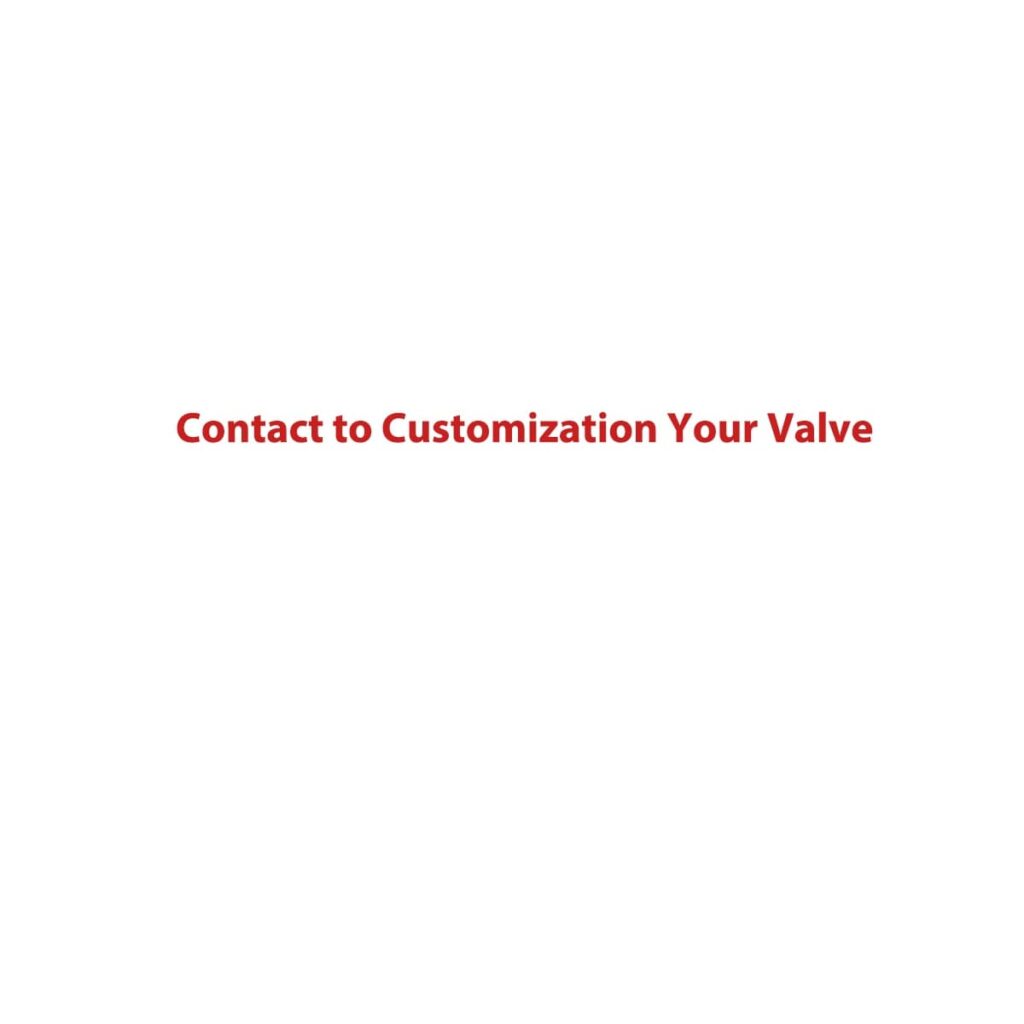
Multi way ball valve
STRUCTURE FEATURES
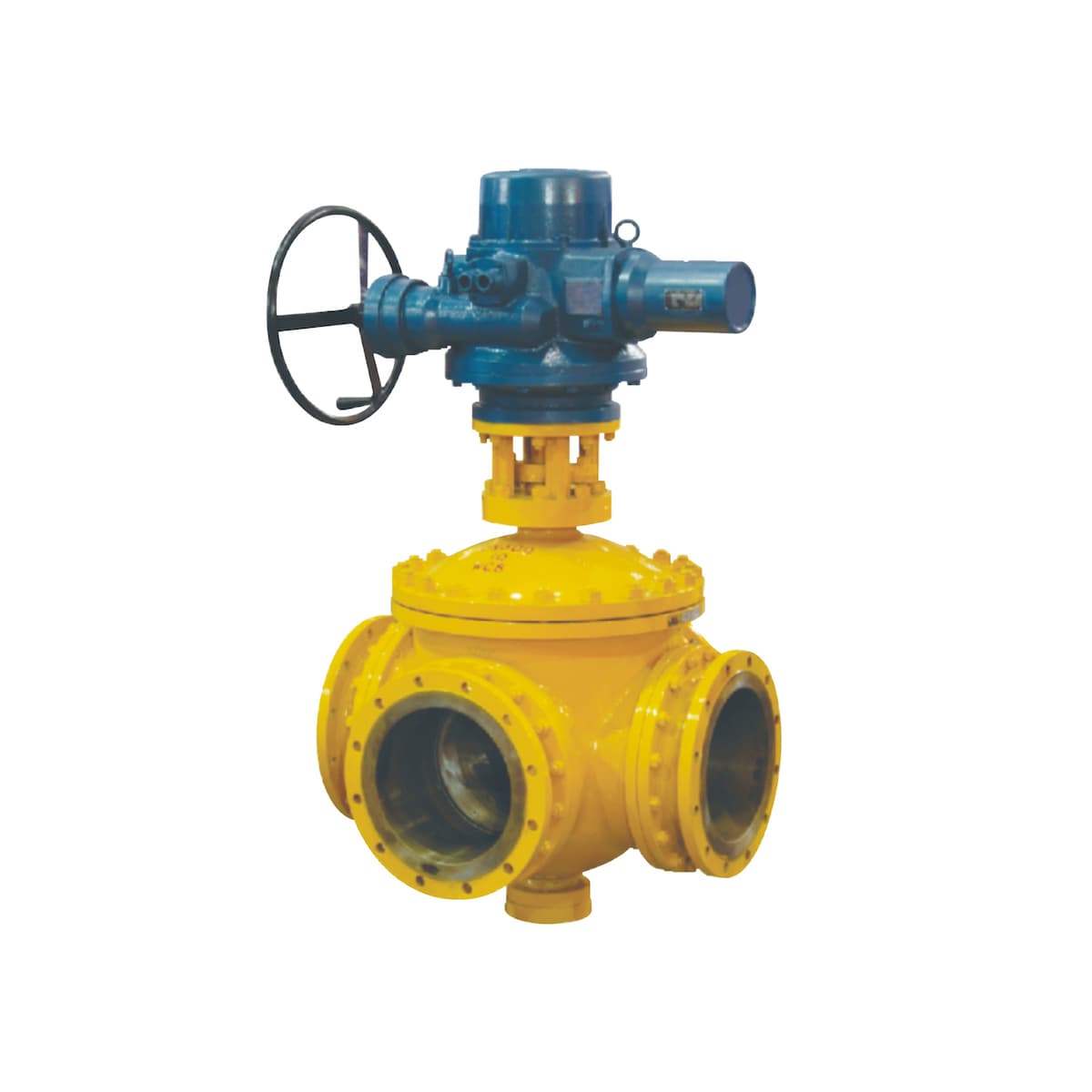
The ball, valve stem, and handle are the moving parts of the valve and are an assembly unit. The head of the valve stem adopts a flat square structure. so that the user can easily and quickly identify the valve in the open or closed state at the position of the handle.
When the handle or flat square of the valve stem is flat with the pipeline axis, the valve is in the open state; when the handle or flat square of the valve stem is perpendicular to the pipeline axis, the valve is in the closed state.
To prevent misoperation of the valve, the valve lock can be used to lock the valve when the valve is fully open or fully closed, especially when the valve is installed in the field or when the process flow does not allow the valve to be opened or closed.
To prevent other personnel from operating the valve by mistake, set the valve position Locking is very important. Therefore, according to the needs of users, the installation of positioning pieces with keyholes in the valve design can meet the safety requirements of users.
Request a FREE quote
we look forward to collaborating with you.